Restoration
6th Update: 26th August 2015
1. The metal glazing bars and door posts, removed in the 1950s to allow garden machinery to enter the greenhouse, have now been completely rebuilt. For this the bars had to be forged at a foundry in Yorkshire matching the pattern of the existing bars and then the shapes sharpened by blacksmiths. The door frames are of cast iron and required a particular mould. There were probably steps up to and down from the original door as the surviving lintel is high. These will not be replaced. The door will be at ground level, though the lintel will be kept for archaeological reasons.
Installing this new metal work requires a good deal of welding and smoothing to obscure the joins. The vertical glazing bars are not parallel to each other, nor are they at the original west end, for reasons we discuss below. The glaziers have to work with these anomalies.
Installing this new metal work requires a good deal of welding and smoothing to obscure the joins. The vertical glazing bars are not parallel to each other, nor are they at the original west end, for reasons we discuss below. The glaziers have to work with these anomalies.
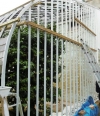
2. The stresses on the building over time will inevitably appear at the corners. Each corner has a cast iron drain pipe. These had to an extent twisted and even cracked to allow the movement of the building out of alignment – not to mention frosting as they blocked with leaves. New down pipes with elegant detailing have been cast, but, as we knew, the gutter outflow is not vertically over the drain; it is about 0.5 inches out, but that is important. These drain pipes, though short, say 3 feet, are visually important verticals and have to cohere to the glazing bars lines.
The answer has been to reconstruct the stone buttresses which carry the pipes. These had, anyway, been messily repaired over the years and looked scruffy. The new buttresses allow for the warping of the metal frame and yet still maintain symmetry of the uprights.
The answer has been to reconstruct the stone buttresses which carry the pipes. These had, anyway, been messily repaired over the years and looked scruffy. The new buttresses allow for the warping of the metal frame and yet still maintain symmetry of the uprights.
3. The glaziers are now here full time, working on the roof, perched on uncomfortable ladders. Original panes, which were removed as loose and numbered, are put back into exactly the same position. Replacement panes, mainly recovered reeded glass, though with some plain glass interspersed (we could not find sufficient narrow reeded supplies) have to be measured individually and cut to size. The cutting, with a tungsten tipped “pen”, is done free hand and is amazingly quick. Shouting down the measurements and going up and down the scaffolding with a pane that can fit in only one space is not. As of today the glaziers have done about a quarter of the roof.
.
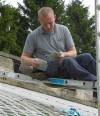
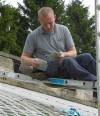